Le fer est un élément familier à chaque personne sur notre planète. Et il n'y a rien d'étonnant à cela. En effet, au regard de sa teneur dans la croûte terrestre (jusqu'à 5 %), ce composant est le plus courant. Cependant, seul un quarantième de ces réserves se trouve dans des gisements propices au développement. Les principaux minerais de fer sont la sidérite, le minerai de fer brun, l'hématite et la magnétite.
Origine du nom
Pourquoi le fer porte-t-il ce nom ? Si nous considérons le tableau des éléments chimiques, alors ce composant y est marqué comme "ferrum". Il est abrégé en Fe.
Selon de nombreux étymologues, le mot "fer" nous vient de la langue proto-slave, dans laquelle il ressemblait à zelezo. Et ce nom vient du lexique des anciens Grecs. Ils ont appelé le métal si célèbre aujourd'hui "le fer".
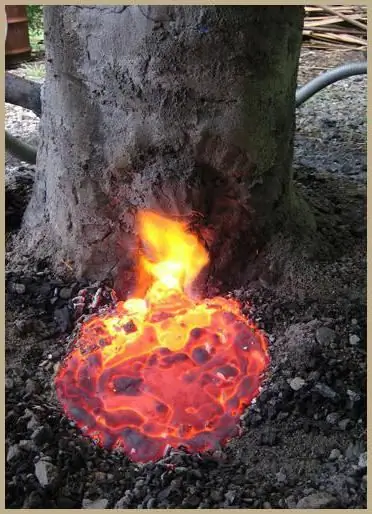
Il existe une autre version. Selon elle, le nom "fer" nous vient du latin, oùsignifiait « étoilé ». L'explication réside dans le fait que les premiers échantillons de cet élément découverts par l'homme étaient d'origine météoritique.
Utilisation du fer
Dans l'histoire de l'humanité, il y a eu une période où les gens accordaient plus de valeur au fer qu'à l'or. Ce fait est enregistré dans l'Odyssée d'Homère, qui dit que les gagnants des jeux organisés par Achille ont reçu, en plus de l'or, un morceau de fer. Ce métal était essentiel pour presque tous les artisans, agriculteurs et guerriers. Et c'est son énorme besoin qui est devenu le meilleur moteur pour la production de ce matériau, ainsi que de nouveaux progrès techniques dans sa fabrication.
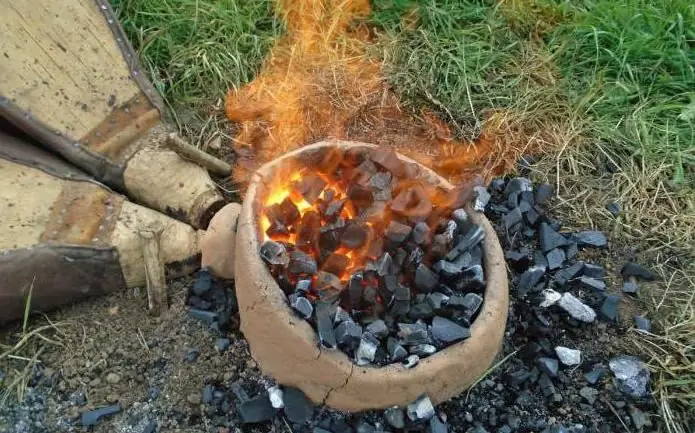
9-7 cc. AVANT JC. considéré comme l'âge du fer dans l'histoire humaine. Au cours de cette période, de nombreuses tribus et peuples d'Asie et d'Europe ont commencé à développer la métallurgie. Cependant, le fer est encore très demandé aujourd'hui. Après tout, c'est toujours le principal matériau utilisé pour la fabrication d'outils.
Produit fromage
Quelle est la technologie de production de bloom fer que l'humanité a commencé à extraire à l'aube du développement de la métallurgie ? La toute première méthode inventée par l'humanité s'appelait la fabrication du fromage. De plus, il a été utilisé pendant 3000 ans, sans changer depuis la fin de l'âge du bronze jusqu'à la période jusqu'au 13ème siècle. Le haut fourneau n'a pas été inventé en Europe. Cette méthode s'appelait raw. Les cornes pour lui étaient construites en pierre ou en argile. Parfois, des morceaux de scories servaient de matériau à leurs murs. La dernière version de la forge de l'intérieur étaitrecouvert d'argile réfractaire, auquel du sable ou de la corne concassée a été ajouté pour améliorer la qualité.
Qu'est-ce qui rend le fer éclair ? Les fosses préparées étaient remplies de minerai «brut» de prairie ou de marais. L'espace de fusion de ces fours était rempli de charbon de bois, qui était ensuite complètement chauffé. Au fond de la fosse se trouvait un trou pour l'alimentation en air. Au début, il était soufflé avec des soufflets à main, qui ont ensuite été remplacés par des soufflets mécaniques.
Dans les toutes premières forges, le tirage naturel était organisé. Elle a été réalisée à travers des trous spéciaux - des buses, situées sur les parois de la partie inférieure du four. Souvent, les anciens métallurgistes assuraient l'alimentation en air grâce à l'utilisation d'une conception permettant d'obtenir l'effet d'un tuyau. Ils ont créé un espace intérieur haut et en même temps étroit. Très souvent, ces fours étaient construits au pied des collines. Ces endroits avaient la plus grande pression de vent naturelle, qui a été utilisée pour augmenter la traction.
À la suite du processus en cours, le minerai a été converti en métal. Dans le même temps, la roche vide coulait progressivement. Des grains de fer se sont formés au fond du four. Ils se sont collés les uns aux autres, se transformant en ce qu'on appelle le "fluage". Il s'agit d'une masse spongieuse lâche imprégnée de scories. Au four, le cracker était chauffé à blanc. C'est dans cet état qu'ils l'ont sorti et l'ont rapidement forgé. Des morceaux de scories viennent de tomber. Ensuite, le matériau résultant a été soudé en une pièce monolithique. Le résultat était du fer flashy. Le produit final avait la forme d'un pain plat.
C'était quoicomposition de fleur de fer? C'était un alliage de Fe et de carbone, qui était très petit dans le produit final (si l'on considère le pourcentage, alors pas plus de centièmes).
Cependant, le fer fleuri que les gens recevaient dans le four à cru n'était pas très dur et durable. C'est pourquoi les produits fabriqués à partir d'un tel matériau ont rapidement échoué. Les lances, les haches et les couteaux étaient tordus et ne restaient pas aiguisés longtemps.
Acier
Dans la production de fer dans les forges, en plus de ses morceaux mous, il y avait aussi ceux qui avaient une dureté plus élevée. Il s'agissait de morceaux de minerai qui étaient en contact étroit avec du charbon de bois pendant le processus de fusion. Un homme a remarqué ce schéma et a commencé à augmenter délibérément la surface en contact avec le charbon. Cela a permis de carburer le fer. Le métal ainsi obtenu a commencé à répondre aux besoins des artisans et de ceux qui utilisaient des produits fabriqués à partir de celui-ci.
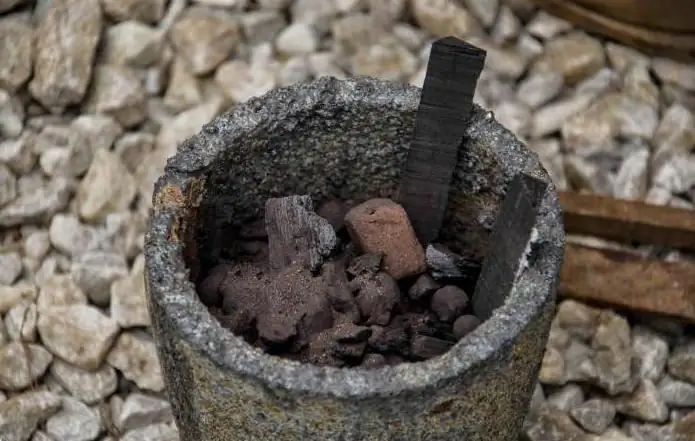
Ce matériau était de l'acier. Il est encore utilisé à ce jour dans la fabrication d'un grand nombre de structures et de produits. L'acier, fondu par d'anciens métallurgistes, est du fer flash, qui contient jusqu'à 2 % de carbone.
L'acier doux existait aussi. C'était du fer flash, qui contenait moins de 0,25% de carbone. Si l'on considère l'histoire de la métallurgie, c'est l'acier doux qui a été produit au stade initial de la production de fromage. Quel est l'autre nom du flash iron ? Il existe également une troisième variété. Lorsqu'il contient plus de 2 % de carbone, alorsc'est de la fonte.
Invention du haut fourneau
La méthode florissante d'obtention de fer à l'aide de forges à sang brut dépendait fortement de la météo. Après tout, pour une telle technologie, il était important que le vent souffle dans le tube fabriqué. C'est le désir de s'éloigner des caprices de la météo qui a poussé une personne à créer des fourrures. C'étaient les appareils nécessaires pour attiser le feu dans le four à cru.
Après l'apparition des soufflets, les forges pour la production de métal ne sont plus construites à flanc de coteau. Les gens ont commencé à utiliser un nouveau type de poêles, appelés "fosses à loups". C'étaient des structures dont une partie était dans le sol et la seconde (maisons) dominait au-dessus sous la forme d'une structure faite de pierres maintenues ensemble par de l'argile. À la base d'un tel four, il y avait un trou dans lequel un tube de soufflet était inséré pour attiser le feu. Le charbon déposé dans la maison a été brûlé, après quoi il a été possible d'obtenir le craquelin. Elle a été tirée à travers le trou, qui s'est formé après le retrait de plusieurs pierres de la partie inférieure de la structure. Ensuite, le mur a été restauré et le four a été rempli de minerai et de charbon pour recommencer.

La production de fer brillant a été constamment améliorée. Au fil du temps, les maisons ont commencé à être construites plus grandes. Cela a nécessité une augmentation de la productivité des mechs. En conséquence, le charbon a commencé à brûler plus rapidement, saturant le fer de carbone.
Fonte
Comment s'appelle le flash fer à haute teneur en carbone ? Comme c'étaitmentionné ci-dessus, c'est la fonte qui est si courante aujourd'hui. Sa caractéristique distinctive est sa capacité à fondre à des températures relativement basses.
Brick iron - fonte sous forme solide - il était impossible de forger. C'est pourquoi les anciens métallurgistes ne lui prêtèrent aucune attention au début. D'un seul coup de marteau, ce matériau s'est tout simplement brisé en morceaux. À cet égard, la fonte, ainsi que les scories, étaient initialement considérées comme des déchets. En Angleterre, ce métal était même appelé "pig iron". Et ce n'est qu'avec le temps que l'on s'est rendu compte que ce produit, bien qu'il soit sous forme liquide, peut être coulé dans des moules pour obtenir divers produits, par exemple des boulets de canon. Grâce à cette découverte aux 14-15 siècles. dans l'industrie ont commencé à construire des hauts fourneaux pour la production de fonte brute. La hauteur de ces structures atteignait 3 mètres ou plus. Avec leur aide, le fer de fonderie a été fondu pour la production non seulement de boulets de canon, mais aussi des canons eux-mêmes.
Développement de la production de hauts fourneaux
Une véritable révolution dans le secteur métallurgique s'est produite dans les années 80 du XVIIIe siècle. C'est alors que l'un des commis de Demidov a décidé que pour une plus grande efficacité dans le fonctionnement des hauts fourneaux, l'air devrait leur être fourni non pas par une, mais par deux buses, qui devraient être situées des deux côtés du foyer. Peu à peu, le nombre de ces buses a augmenté. Cela a permis d'uniformiser le processus de soufflage, d'augmenter le diamètre du foyer et d'augmenter la productivité des fours.
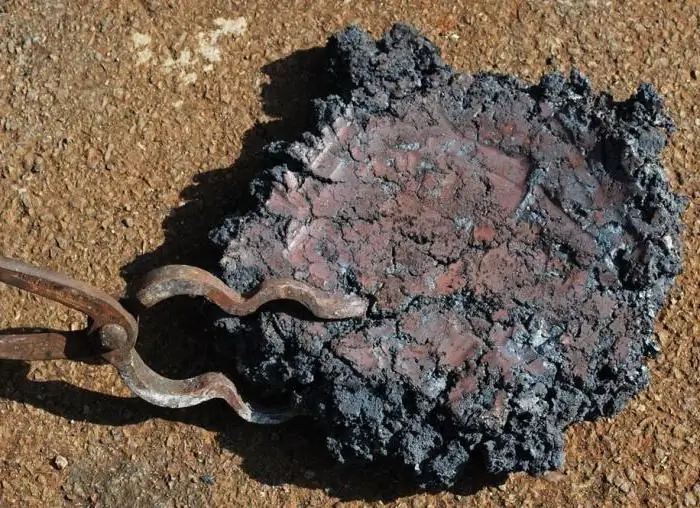
Le développement de la production de hauts fourneaux a également été facilité par le remplacement du charbon de bois,pour lesquels les forêts ont été abattues, pour le coke. En 1829, en Ecosse, à l'usine de Clayde, de l'air chaud est soufflé pour la première fois dans le haut fourneau. Une telle innovation a considérablement augmenté la productivité du four et réduit la consommation de combustible. De nos jours, le processus de haut fourneau a été amélioré en remplaçant une partie du coke par du gaz naturel, dont le coût est encore plus faible.
Bulat
Comment s'appelle le flash de fer, qui possède des propriétés uniques qui ont été utilisées dans la fabrication d'armes ? Nous connaissons ce matériau sous le nom d'acier damassé. Ce métal, comme l'acier de Damas, est un alliage de fer et de carbone. Cependant, contrairement à ses autres espèces, c'est un fer flashy avec de bonnes qualités. Il est résistant et dur, et également capable de produire un tranchant exceptionnel dans la lame.
Les métallurgistes de nombreux pays tentent de percer le secret de la production d'acier damassé depuis plus d'un siècle. Un grand nombre de recettes et de méthodes ont été proposées qui comprenaient l'ajout d'ivoire, de pierres précieuses, d'or et d'argent au fer. Cependant, le secret de l'acier damassé n'a été révélé que dans la première moitié du XXe siècle par le remarquable métallurgiste russe P. P. Anosov. Ils ont pris du fer fleuri, qui a été déposé dans un four à charbon de bois, où brûlait un feu ouvert. Le métal fondit, saturé de carbone. A cette époque, il était recouvert de scories de dolomie cristalline, parfois avec l'ajout de la calamine la plus pure. Sous une telle couche, le métal était très intensément libéré du silicium, du phosphore, du soufre et de l'oxygène. Cependant, ce n'était pas tout. L'acier résultant devait être refroidi autant que possibleplus lent et plus calme. Cela a permis de former, tout d'abord, de gros cristaux ayant une structure ramifiée (dendrites). Ce refroidissement a eu lieu directement dans le foyer, qui était rempli de charbon ardent. À l'étape suivante, un forgeage habile a été effectué, au cours duquel la structure résultante ne devrait pas s'effondrer.
Les propriétés uniques de l'acier damassé ont ensuite trouvé une explication dans les travaux d'un autre métallurgiste russe D. K. Chernov. Il a expliqué que les dendrites sont en acier réfractaire mais relativement doux. L'espace entre leurs "branches" dans le processus de solidification du fer est rempli de carbone plus saturé. C'est-à-dire que l'acier doux est entouré d'acier plus dur. Cela explique les propriétés de l'acier damassé, contenues dans sa viscosité et en même temps sa haute résistance. Un tel hybride d'acier lors de la fusion conserve sa structure arborescente, le transformant uniquement d'une ligne droite en une ligne en zigzag. La particularité du motif résultant dépend dans une large mesure de la direction des coups, de la force, ainsi que de l'habileté du forgeron.
Acier de Damas
Dans les temps anciens, ce métal était le même acier damassé. Cependant, un peu plus tard, l'acier de Damas a commencé à être appelé un matériau obtenu par forgeage à partir d'un grand nombre de fils ou de bandes. Ces éléments étaient en acier. De plus, chacun d'eux était caractérisé par une teneur en carbone différente.
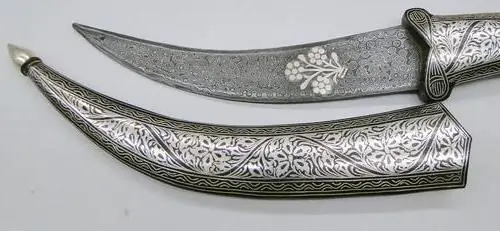
L'art de fabriquer un tel métal a atteint son plus grand développement au Moyen Âge. Par exemple, dans la structure de la lame japonaise bien connue, les chercheurs ont trouvéenviron 4 millions de fils d'acier d'épaisseur microscopique. Cette composition a rendu le processus de fabrication des armes très laborieux.
Production dans des conditions modernes
Les anciens métallurgistes ont laissé un échantillon de leurs compétences, pas seulement dans le domaine des armes. L'exemple le plus frappant de fer fleuri pur est la célèbre colonne située près de la capitale de l'Inde. Les archéologues ont déterminé l'âge de ce monument de l'art métallurgique. Il s'est avéré que la colonne avait été construite il y a encore 1,5 mille ans. Mais le plus surprenant réside dans le fait qu'il est aujourd'hui impossible de détecter même de petites traces de corrosion à sa surface. Le matériau de la colonne a été soumis à un examen minutieux. Il s'est avéré qu'il s'agit de fer flash pur, qui ne contient que 0,28% d'impuretés. Une telle découverte stupéfia même les métallurgistes modernes.
Au fil du temps, le fer flashy a progressivement perdu de sa popularité. Le métal fondu dans un four à foyer ouvert ou dans un haut fourneau a commencé à bénéficier de la plus grande demande. Cependant, lors de l'application de ces procédés, on obtient un produit de pureté insuffisante. C'est pourquoi la méthode la plus ancienne de production de ce matériau a récemment reçu sa seconde vie, ce qui permet de produire du métal avec les caractéristiques de qualité les plus élevées.
Comment s'appelle le flash iron aujourd'hui ? Il nous est familier en tant que métal de réduction directe. Bien sûr, le fer fleuri d'aujourd'hui n'est pas produit de la même manière que dans les temps anciens. Pour sa production, les technologies les plus modernes sont utilisées. Ils permettent de produire un métal qui n'a pratiquement pasimpuretés étrangères. Les fours tubulaires rotatifs sont utilisés dans la production. Ces éléments structuraux sont utilisés pour la cuisson de divers matériaux en vrac à haute température dans l'industrie chimique, la cimenterie et de nombreuses autres industries.
Comment s'appelle désormais le flash iron ? Il est considéré comme pur et est utilisé pour obtenir une méthode qui n'est essentiellement pas très différente de celle qui existait dans les temps anciens. Pourtant, les métallurgistes utilisent du minerai de fer, qui est chauffé lors du processus d'obtention du produit final. Cependant, aujourd'hui, les matières premières sont initialement soumises à un traitement supplémentaire. Il s'enrichit, créant une sorte de concentré.
L'industrie moderne utilise deux méthodes. Les deux vous permettent d'obtenir du fer flash à partir de concentré.
La première de ces méthodes consiste à amener les matières premières à la température requise à l'aide de combustibles solides. Un tel processus est très similaire à celui réalisé par les anciens métallurgistes. Au lieu de combustible solide, on peut utiliser du gaz, qui est une combinaison d'hydrogène et de monoxyde de carbone.
Qu'est-ce qui précède l'obtention de ce matériel ? Comment s'appelle le flash iron aujourd'hui ? Après avoir chauffé le concentré de minerai de fer, les boulettes restent dans le four. C'est à partir d'eux que le métal pur est ensuite produit.
La deuxième méthode utilisée pour restaurer le fer est très similaire technologiquement à la première. La seule différence est que les métallurgistes utilisent de l'hydrogène pur comme combustible pour chauffer le concentré. Avec cette méthode, le fer est obtenu beaucoup plus rapidement. Exactementpar conséquent, il se distingue par une qualité supérieure, car dans le processus d'interaction de l'hydrogène avec du minerai enrichi, seules deux substances sont obtenues. Le premier est du fer pur et le second est de l'eau. On pourrait supposer que cette méthode est très populaire dans la métallurgie moderne. Cependant, aujourd'hui, il est rarement utilisé et, en règle générale, uniquement pour la production de poudre de fer. Cela s'explique par le fait qu'il est assez difficile d'obtenir de l'hydrogène pur, tant en termes de résolution de problèmes techniques qu'en raison de difficultés économiques. Le stockage du carburant reçu est également une tâche difficile.
Relativement récemment, des scientifiques ont mis au point une troisième méthode de production de fer réduit. Il s'agit d'obtenir du métal à partir de concentré de minerai, sans passer par l'étape de sa transformation en boulettes. Des études ont montré qu'avec cette méthode, le fer pur peut être produit beaucoup plus rapidement. Cependant, cette méthode n'a pas encore été mise en œuvre dans l'industrie, car elle nécessite des changements technologiques importants et un changement d'équipement des entreprises de la métallurgie.
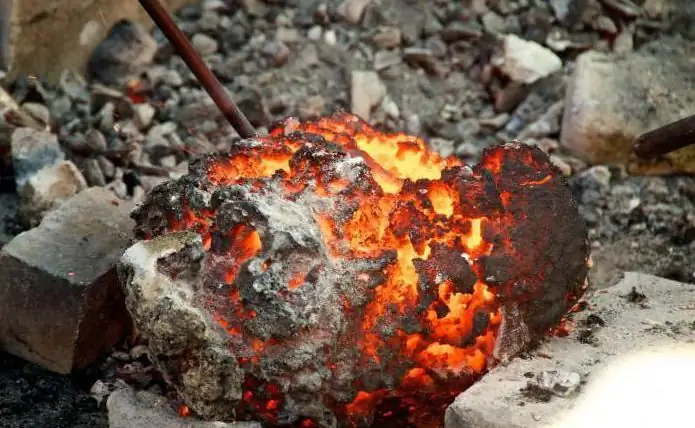
Comment s'appelle le flash iron aujourd'hui ? Ce matériau nous est familier en tant que métal de réduction directe, parfois aussi appelé spongieux. Il s'agit d'un matériau économique, de haute qualité et respectueux de l'environnement qui ne contient pas d'impuretés de phosphore et de soufre. En raison de ses caractéristiques, le fer fleuri est utilisé dans les industries mécaniques (aviation, construction navale et instrumentation).
Fechral
Comme vous pouvez le voir, aujourd'hui, lorsque vous utilisezles technologies les plus modernes utilisent des matériaux tels que le fer fleuri. Fechral est également un alliage recherché. En plus du fer, il contient des composants tels que le chrome et l'aluminium. Le nickel est également présent dans sa structure, mais pas plus de 0,6 %.
Fechral a une bonne résistance électrique, une dureté élevée, fonctionne très bien avec les céramiques à haute teneur en alumine, n'a pas tendance à piquer et résiste à la chaleur dans une atmosphère contenant du soufre et ses composés, de l'hydrogène et du carbone. Mais la présence de fer dans l'alliage le rend assez fragile, ce qui rend difficile le traitement du matériau dans la fabrication de divers produits.
Fechral est utilisé dans la fabrication d'éléments chauffants pour fours de laboratoire et industriels, dont la température de fonctionnement maximale est de 1400 degrés. Parfois, des pièces de cet alliage sont utilisées à d'autres fins. Ils sont placés dans les appareils de chauffage domestiques, ainsi que dans les appareils électriques à action thermique. Fechral a été largement utilisé dans la production de cigarettes électroniques. Aussi, un alliage de fer, d'aluminium et de chrome est recherché dans le domaine de la fabrication d'éléments résistifs. Il peut s'agir, par exemple, de résistances de démarrage-freinage de locomotives électriques.
Fechral est utilisé pour produire du fil, ainsi que du fil et du ruban. Parfois, des cercles et des tiges en sont obtenus. Tous ces produits sont utilisés dans la fabrication de diverses formes de résistances pour fours électriques.