Parlons du rôle du coke dans le processus de haut fourneau. Examinons de plus près l'essence de cette production métallurgique.
Aujourd'hui, le fer et l'acier sont fabriqués à l'aide du procédé de haut fourneau, dans lequel le four est un élément important.
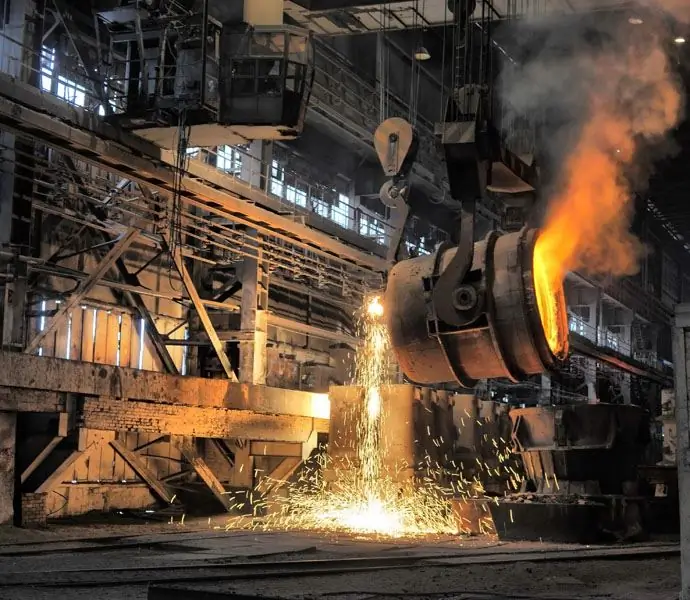
Spécificités de l'unité
Considérez les caractéristiques de l'appareil, son objectif. Les principaux processus du haut fourneau sont associés à la fusion du coke. C'est un matériau poreux qui est fritté à partir d'une masse de carbone obtenue par calcination du charbon sans la présence d'oxygène atmosphérique.
Un haut fourneau est une unité puissante et performante, où une quantité importante de vent et de charge est consommée.
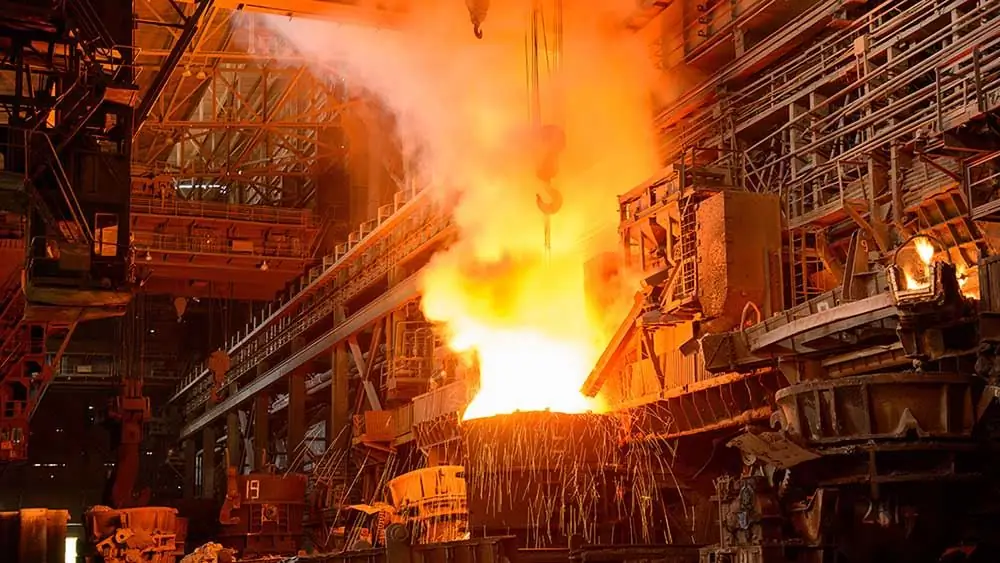
Chargement des matières premières
Le haut fourneau moderne nécessite que les matériaux y restent pendant 4 à 6 heures, les substances gazeuses - 3 à 12 secondes. Si les gaz sont complètement répartis sur la section transversalefours, vous pouvez compter sur des taux de fusion élevés, la production de fer est en cours. Le procédé de haut-fourneau consiste à prendre en compte le mouvement des gaz à travers des zones qui ont une résistance de charge plus faible. Par conséquent, lorsqu'il est chargé dans le four, un ajustement est effectué, une redistribution du coke et de l'aggloméré sur la section transversale du four afin qu'ils diffèrent par leur perméabilité aux gaz. Sinon, un plus grand pourcentage de gaz quittera le four avec une température importante, ce qui affectera négativement l'utilisation de l'énergie thermique, le processus de haut fourneau ne sera pas pleinement efficace.
Dans les zones à haute résistance, le mélange gazeux passera légèrement chauffé, une chaleur supplémentaire sera nécessaire dans la partie inférieure du four, par conséquent, la consommation de matières premières augmentera considérablement.
Quelles sont les autres fonctionnalités importantes à prendre en compte lors du téléchargement ? Le procédé de haut-fourneau pour produire de la fonte brute est une production énergivore. C'est pourquoi une couche d'agglomérat moins perméable au gaz est utilisée près des parois du four, et une couche de coke est augmentée au centre, grâce à quoi le flux de gaz est redistribué vers le centre. Les matériaux sont régulièrement espacés autour de la circonférence.
La charge est chargée en portions séparées - flux. Une portion se compose de plusieurs bennes, partie minerai (agglomérat), coke. Le rapport des ingrédients d'origine est déterminé par des experts.
Le procédé de haut-fourneau permet une co-alimentation en matières premières, dans laquelle les bennes de coke et d'agglomération sont collectées sur un grand cône puis chargées dans un four.
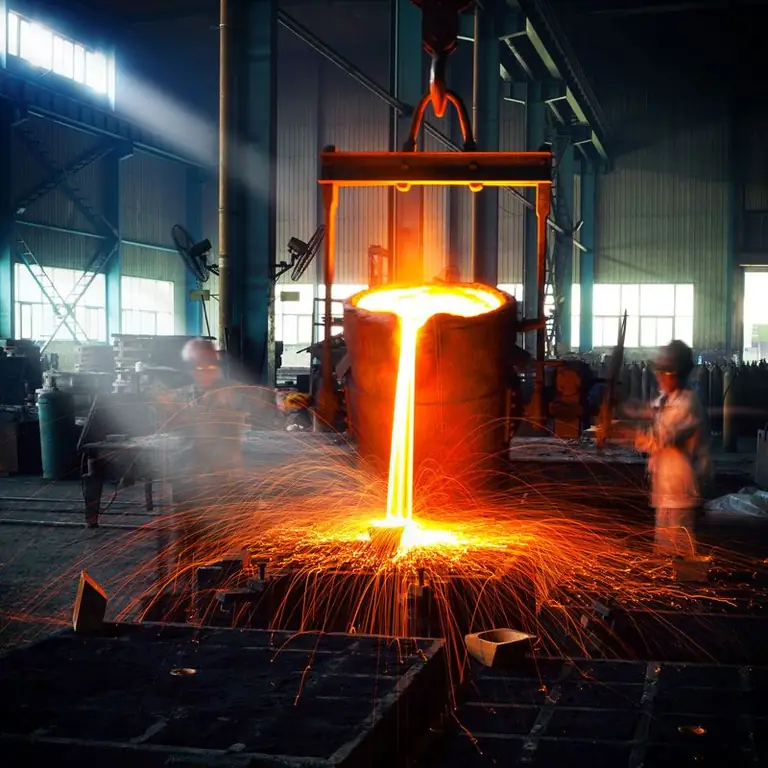
Ajustement de la distribution par lots
La répartition du coke et de l'agglomérat sur la section transversale des sommets est contrôlée par les méthodes suivantes:
- modifier l'ordre des matières premières sur le grand cône;
- les services partagés et partagés s'appliquent;
- des plaques mobiles sont installées près des murs du haut.
Le procédé haut-fourneau implique la prise en compte de certaines régularités pour l'introduction des matériaux en vrac:
- pose de matières premières tombant d'un grand cône sur un sommet avec une élévation - un peigne;
- Au sommet (au point de chute) de la charge, les fines s'accumulent, les gros morceaux roulent jusqu'au pied de la crête, donc, dans cette zone, la perméabilité au gaz de la charge est plus grande;
- la crête est affectée par le niveau de remblai au sommet, ainsi que la distance avec un grand cône;
- le gros cône ne descend pas complètement, donc de petits morceaux de coke arrivent à la périphérie.
Le centre du four reçoit principalement le matériau des bennes d'alimentation, qui ont été les dernières à être chargées dans le grand cône. Si vous modifiez l'ordre de chargement, vous pouvez obtenir une redistribution des matériaux sur la section transversale du plateau.
Pour contrôler le processus de répartition de la charge utilisée sur le volume du four, deux appareils à cône sont utilisés. Récemment, certains hauts fourneaux sont équipés de plaques mobiles près des parois du sommet, ce qui vous permet de modifier l'angle d'inclinaison, de les déplacer le long d'un plan horizontal.
Les morceaux de la charge qui tombent sur les plaques sont réfléchis par celles-ci, ce qui vous permet de diriger la matière première vers certaines zones du dessus.
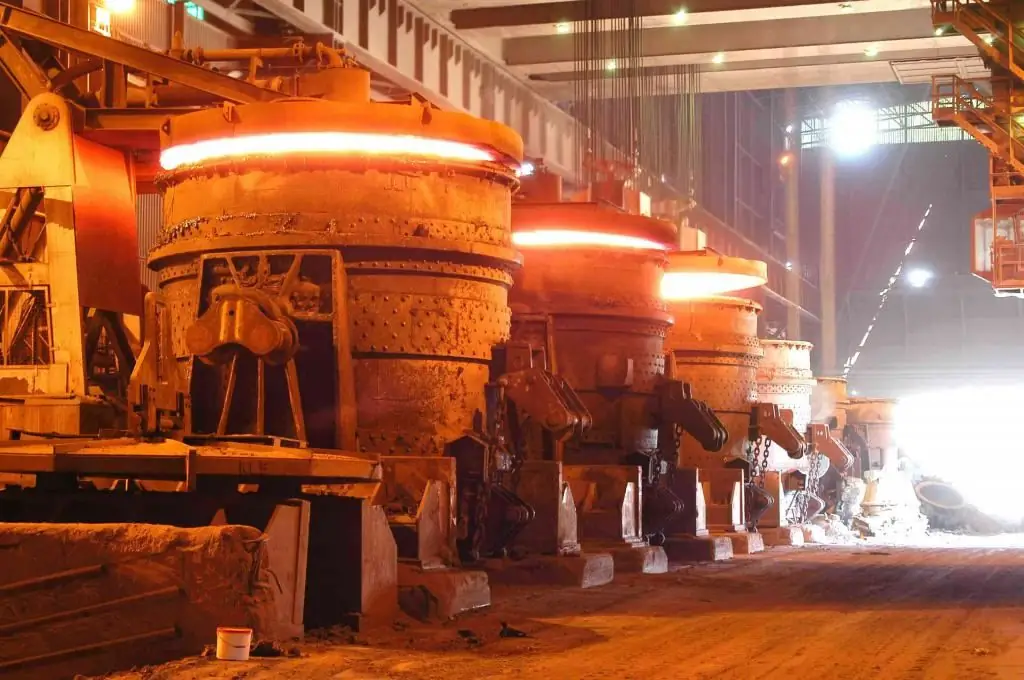
Options de poêlepas de conicité
Dans les fours dépourvus de dispositif de chargement à cône, le chargement des matières premières s'effectue à travers deux trémies sas qui s'ouvrent alternativement. Les matières premières leur sont livrées par des convoyeurs à bande inclinés, sur lesquels le coke et l'aggloméré sont situés à intervalles clairs. Une partie vient du tapis dans une trémie, puis elle est déchargée sur le haut du four le long d'un plateau incliné rotatif. Pendant la période de déchargement, ils effectuent une dizaine de tours complets autour de l'axe central fixe.
Cycle de charge
Il est d'usage de l'appeler un nombre répétitif de lots de matériaux de charge. La portion maximale est déterminée par le volume de la trémie de verrouillage du mécanisme de chargement. Le nombre de portions dans un cycle peut aller de 5 à 14. Comment obtenir pleinement les produits du processus de haut fourneau? Afin de répondre à cette question, examinons de plus près l'essence du processus. Avec une teneur accrue en dioxyde de carbone dans le mélange, la basse température contribue à l'intégralité de l'échange de chaleur et des processus chimiques dans le haut fourneau. Pour que l'appareil fonctionne de manière économique et intensive, la teneur quantitative en dioxyde de carbone le long de l'axe et à la périphérie du four doit être réduite et à une hauteur d'un ou deux mètres des murs - augmentée.
Le contrôle de la température dans les nouveaux fours est effectué en introduisant des sondes à travers des trous dans le boîtier. Le contrôle du niveau de remplissage en haut est obligatoire pour tous les processus.
Parmi les innovations figure l'utilisation de méthodes de mesure de niveau sans contact basées sur les lectures de capteurs à micro-ondes et infrarouges.
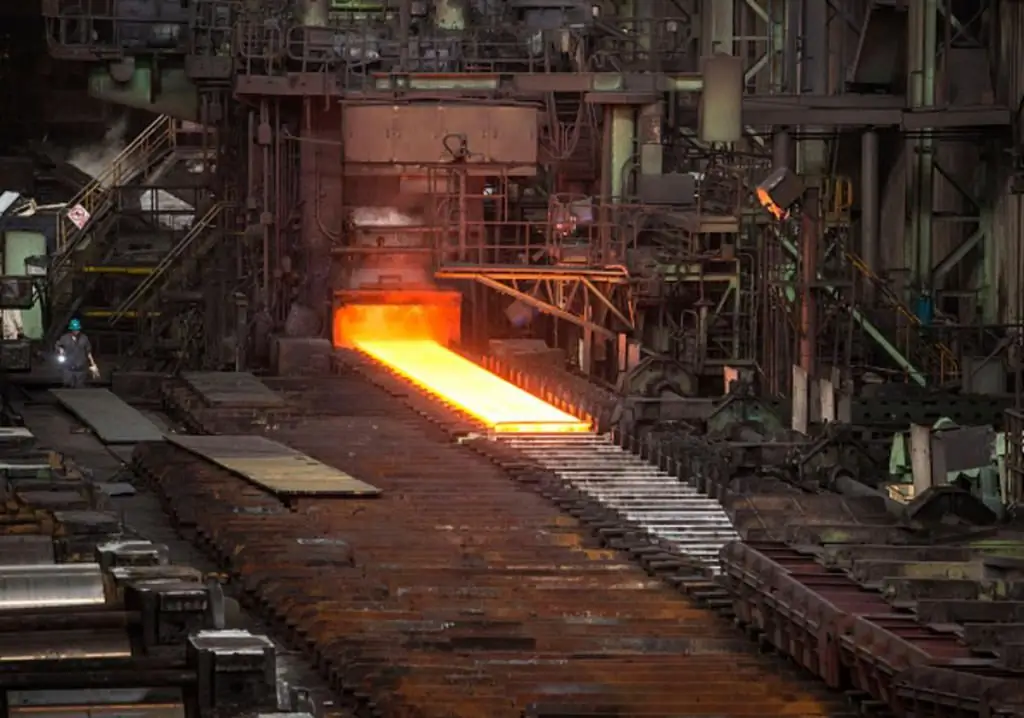
Caractéristiques de distribution de température
En plus de la chaleur introduite par le souffle chauffé, en tant que principale source de chaleur pour le chauffage des gaz et de la charge, effectuant la récupération et compensant les pertes de chaleur, il est possible de compenser les pertes avec la chaleur dégagée lors de la combustion du combustible dans la partie supérieure du foyer. Au fur et à mesure que les produits gazeux remontent du foyer, la chaleur descend vers les matériaux froids chargés et un échange de chaleur se produit. Un processus similaire explique la chute de température de 1400 à 200 degrés à la sortie du haut du four.
Éliminer l'excès d'humidité
Considérons les principaux processus physiques et chimiques dans un haut fourneau. Dans la charge chargée dans le haut fourneau, il y a de l'humidité hygroscopique. Par exemple, dans la composition du coke, sa teneur peut aller jusqu'à 5%. L'humidité s'évapore rapidement sur le dessus, donc une chaleur supplémentaire est nécessaire pour l'enlever.
L'humidité hydratée apparaît lorsque le minerai de fer brun et le kaolin sont chargés dans le haut fourneau. Pour résoudre le problème de la production de fer moderne, ces minerais ne sont pratiquement pas utilisés comme matières premières.
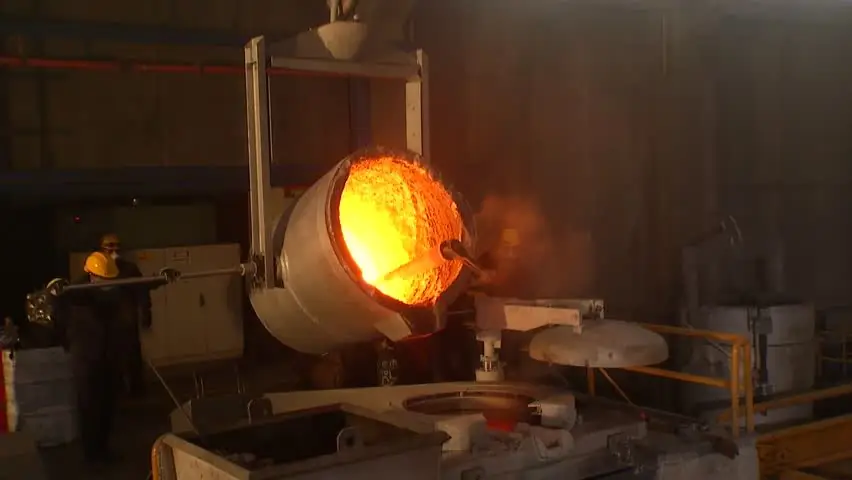
Processus de décomposition des carbonates
Les sels d'acide carbonique peuvent pénétrer dans le haut fourneau. En s'échauffant, ils se décomposent en oxydes de calcium et de carbone, et le processus s'accompagne de la libération d'une quantité suffisante d'énergie.
Récemment, presque aucun minerai n'a été chargé dans les hauts fourneaux. Quel est le rôle des fondants dans le procédé de haut fourneau ? Ils augmentent son efficacitépermettent de réduire les coûts de production. Grâce à l'utilisation d'un fritté fluxé, l'élimination complète du calcaire de la charge du haut-fourneau permet de réaliser d'importantes économies de coke. Le processus de décomposition du calcaire lors de l'agglomération est assuré par la combustion de carburant de qualité inférieure.
Récupération du fer
Le fer est introduit dans le haut fourneau sous forme d'oxydes. L'objectif principal du procédé est de maximiser l'extraction du fer des oxydes par réduction. L'essence du processus est d'éliminer l'oxygène, le carbone, le monoxyde de carbone, l'hydrogène sont utilisés pour cela. La réduction avec du carbone est appelée un processus direct et la réaction avec des substances gazeuses est appelée une interaction indirecte. Quelles sont leurs caractéristiques distinctives ? Dans la réaction directe, le carbone est consommé, ce qui réduit considérablement sa quantité. Le deuxième type de réduction du fer à partir d'oxydes nécessite une quantité excessive d'hydrogène.
Le processus produit du fer solide. Le degré de récupération de la fonte est de 99,8 %. Ainsi, seulement 0,2 à 1 % se transforment en scories.
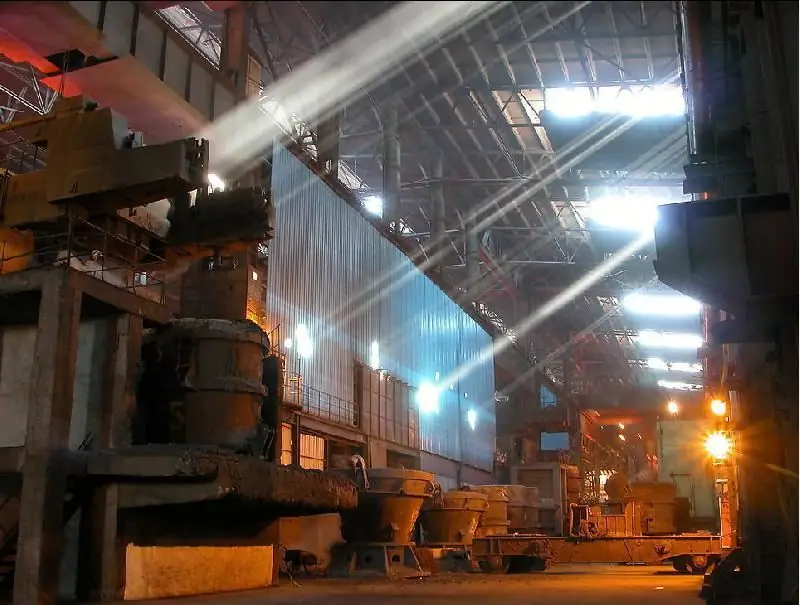
Fonte de fonte au manganèse
Lors du processus de fusion de la fonte remanufacturée, le manganèse entre dans le haut fourneau sous la forme d'un agglomérat. Dans certaines quantités, les minerais de manganèse sous forme de silicates de manganèse contribuent à la production de fonte au manganèse.
La récupération des oxydes de manganèse se fait par étapes. Afin de terminer le processus, des températures élevées doivent être réglées dans le four. Le processus de fusion de la fonte brute s'accompagne deréduction du manganèse uniquement dans un rapport de 55 à 65%. À l'heure actuelle, en raison de la rareté des minerais de manganèse et du manganèse, une petite quantité de fonte au manganèse a été utilisée dans la chaîne technologique. Lors du passage à des fontes à faible teneur en manganèse, il est possible d'économiser non seulement le manganèse lui-même, mais également le coke, car sa consommation pour la réduction directe du métal diminuera.
Conclusion
Le processus de haut fourneau est l'une des principales méthodes de fusion du fer et de l'acier. Selon les composants introduits dans le mélange initial, différents types de produits finis sont actuellement obtenus. Parmi les domaines d'application de la fonte et de l'acier résultants, nous distinguons: la construction mécanique, l'industrie chimique, la médecine, la fabrication d'instruments.