Le moule à froid est un moule réutilisable pour couler le métal. Il peut être détachable (composé de deux parties) ou non (moule à secouer). Le moulage sous pression présente un certain nombre d'avantages par rapport au moulage en coquille, mais il existe également certains inconvénients, par exemple, lors de la coulée de fonte, les pièces moulées nécessitent un traitement thermique supplémentaire.
Avantages
Lors de la formation d'une coulée, il y a un transfert de chaleur intense du métal en fusion vers le moule. Il en résulte une densité plus élevée, de meilleures propriétés mécaniques du métal, une plus grande précision, une meilleure structure et moins de rugosité par rapport aux moulages au sable.
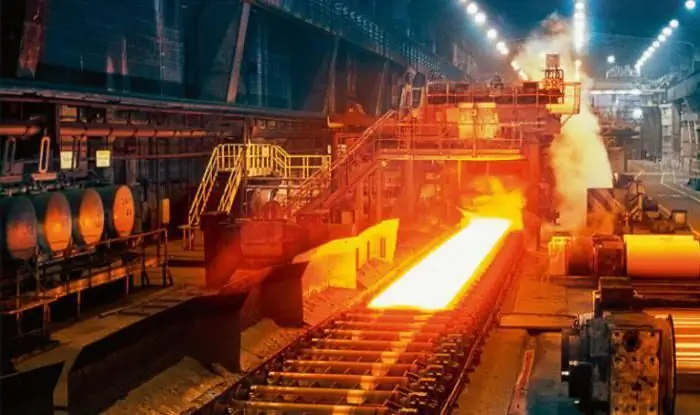
Le processus de moulage en moule est également différent en ce que le moule métallique (moule de refroidissement) peut être réutilisé. Il est fabriqué dans un matériau à haute résistance, grâce auquel la surface de travail du moule est réalisée avec plus de précision. Cela améliore la qualité de surface des pièces moulées et, en raison de la conductivité thermique élevée du moule, les pièces moulées se solidifient rapidement.
Un autre avantage du moulage sous pression par rapport aux moules en sable est que les moulages résultants sont moins traités mécaniquement, ce qui réduit la consommation de matériaux de moulage.
Santé et écologie
Le moulage à froid augmente la productivité du travail de 2 à 3 fois, car à partir du processusles opérations chronophages telles que la préparation du mélange, le nettoyage et le moulage des produits sont exclues. Étant donné que la zone de production diminue également, le coût de réparation et de construction de nouveaux ateliers diminue considérablement.
De nombreuses opérations de travail malsaines sont éliminées du processus, telles que le cognement des moules, le nettoyage des pièces moulées et l'écaillage. Cela contribue non seulement à améliorer les conditions de travail, mais aussi à réduire la pollution de l'environnement.
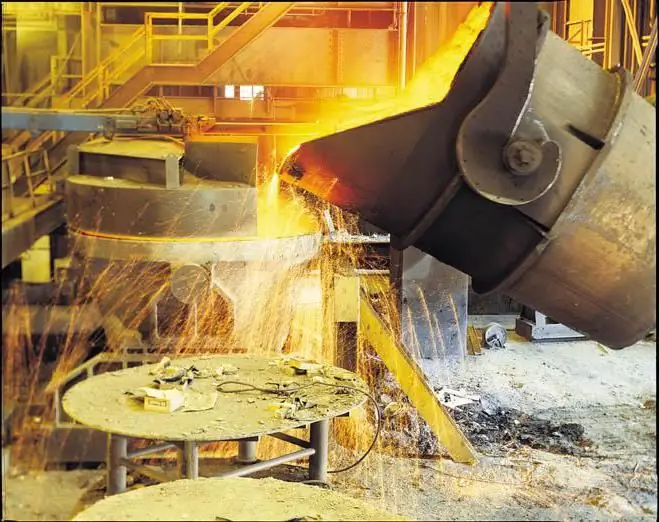
Défauts
La production d'un moule de refroidissement est assez coûteuse en raison de la complexité du processus lui-même. S'il y a des contre-dépouilles dans les pièces moulées, le coût du moule augmente en raison de la nécessité de compliquer la conception: des inserts, du sable jetable et des tiges métalliques fendues sont utilisés.
La durée de vie d'un moule est déterminée par le nombre de moulages de bonne qualité qui peuvent y être obtenus. La stabilité de la forme détermine la faisabilité économique du procédé, notamment dans le procédé de coulée d'acier et de fonte. L'augmentation de la durée de vie des moules est l'un des principaux défis technologiques dans ce domaine de la production.
En raison du refroidissement et de l'épaississement rapides de la masse fondue, il est difficile d'obtenir des produits longs à parois minces lors de la coulée dans un moule. Cela amène également la fonte à acquérir une couche dure et blanchie. La forme est malléable, ce qui peut entraîner des contraintes et des fissures dans les pièces moulées. Lors de l'utilisation de noyaux de sable jetables, la précision des moulages diminue, la rugosité de la surface augmente au point de contact avec le noyau.
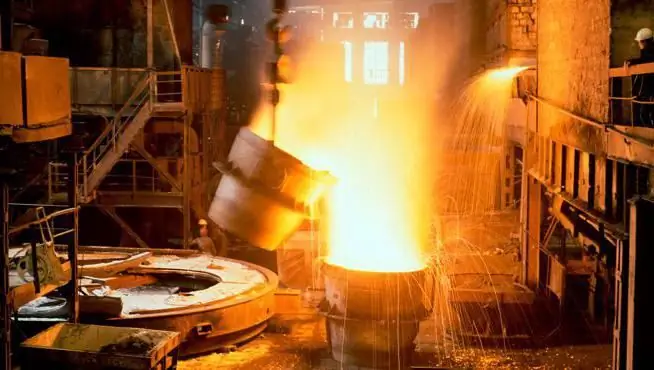
Pièces moulées de qualité
Le moulage et le moule interagissent avec une grande efficacité. La coulée durcit et refroidit dans le moule en sable beaucoup plus longtemps que dans le moule, cependant, la capacité de remplissage du moule en sable est généralement meilleure, ce qui rend le processus de production par coulée en moule de pièces coulées non fluides plus laborieux, et impose également des restrictions sur ces paramètres tels que la taille de la coulée et l'épaisseur minimale des parois. L'aluminium moulé sous pression (ainsi que le cuivre et d'autres métaux non ferreux) est le plus populaire en Russie.
Cependant, grâce à un refroidissement rapide, une structure non poreuse à grain fin peut être obtenue, ce qui augmente non seulement la résistance, mais également la ductilité de la pièce coulée résultante. Lors de la fabrication de produits en fonte par coulée à froid, un certain nombre de problèmes se posent: en raison de la cristallisation particulière des pièces moulées, la formation de carbures, l'eutectique ferrite-graphite est possible. Cela réduit la ténacité et la résistance à l'usure de la fonte. La couche de surface blanchie de ces pièces moulées est très dure, de sorte que les produits ne peuvent être coupés qu'après un traitement thermique (recuit), ce qui élimine le refroidissement.
Structure de la forme
Le moule de refroidissement est, en règle générale, deux demi-moules qui sont fixés avec des pinces (goupilles), et immédiatement avant le début de la coulée du métal en fusion, les demi-moules sont fixés avec des serrures. Les bénéfices alimentent la coulée à travers les soi-disant évents et bouchons d'évent. Les moules en métal sans fonction de connecteur sont appelés moules à secouer.
Avant de verser, la surface de travail du mouletraité avec une couche d'une substance qui protège le moule des chocs thermiques d'une forte augmentation de la température. Cette mesure empêche également le moulage de se gripper avec le moule.
Acier et fonte
Le moulage sous pression de l'acier et de la fonte se fait à l'aide de poudre de quartz, de graphite, de verre soluble et d'argile réfractaire comme revêtement réfractaire. Avant de couler, le moule doit être chauffé à une certaine température, qui dépend de l'épaisseur de la paroi de la pièce coulée et de l'alliage utilisé.
La principale exigence à laquelle le matériau du moule doit répondre est la résistance aux chocs thermiques, inévitable lors de la coulée de métal en fusion. Pour la fabrication de moules, on utilise de la fonte grise, de la fonte ductile, de l'acier de construction, au carbone et allié, ainsi que des alliages de cuivre et d'aluminium.
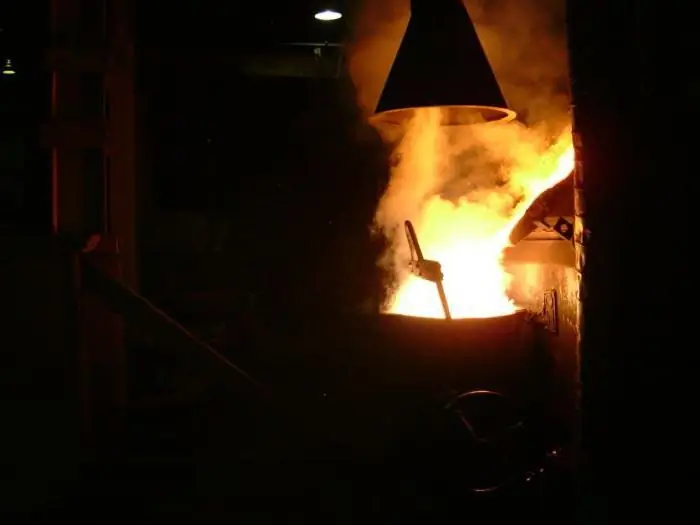
Moule de refroidissement doublé
Il s'agit d'un type de technologie qui combine les avantages du moulage en coquille et sous pression, tandis que les inconvénients des deux méthodes sont atténués. Cette technologie se caractérise non seulement par sa résistance aux fissures, mais également par sa ductilité, ce qui permet de produire des pièces moulées de haute précision et, par rapport à la fonte en coquille, la consommation de matériaux de moulage coûteux est minimale.
Le moule en métal doublé est fabriqué en remplissant l'espace entre le modèle en métal du moulage et la surface intérieure du moule. Les méthodes de sablage et de gelée les plus couramment utilisées. Pour le remplissage, un mélange sable-résine est pris, dans lequel le liant est une résine phénol-formaldéhyde (2-2,6%) eturotropine (environ 10% en poids), ainsi que des composés autodurcissants (liant - verre liquide) et céramiques (liant - silicate d'éthyle). Le moule de refroidissement et le modèle de coulée, ayant une température de 200 degrés, transfèrent la chaleur du mélange, qui durcit et forme une couche de revêtement de 3 à 5 mm d'épaisseur. Des tiges ordinaires ou en coquille sont utilisées pour faire des cavités dans les pièces moulées.
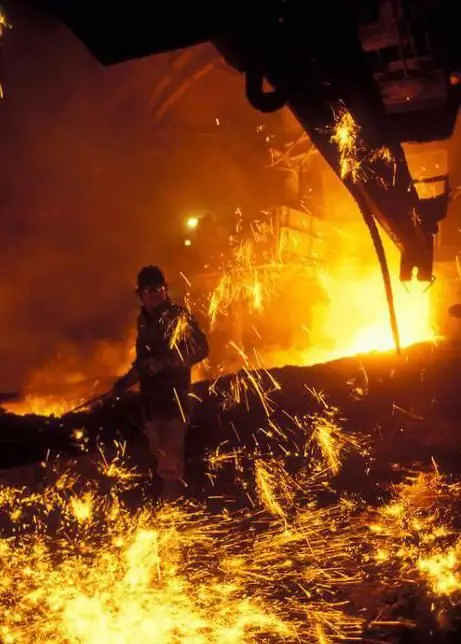
Processus de casting
Le moule de refroidissement, recouvert d'une couche de matériau réfractaire, chauffe. La température de fonctionnement doit être d'au moins deux cents degrés, mais dépend non seulement de l'alliage utilisé pour la coulée, mais également des dimensions de la coulée, de son épaisseur de paroi et des propriétés qui lui sont demandées. Après chauffage, des tiges, de la céramique ou du sable peuvent être installées dans le moule, si cela est bien sûr requis selon le plan de coulée, puis les moitiés du moule sont connectées et étroitement verrouillées avec des pinces spéciales. Si la coulée a lieu dans une machine à mouler, son propre mécanisme de verrouillage du moule est utilisé. Après ces mesures préparatoires, le métal en fusion peut être versé dans le moule de refroidissement.
Lorsque le moulage a déjà acquis une certaine résistance, les tiges métalliques peuvent en être partiellement retirées. Cela facilite ensuite le retrait final des noyaux des pièces moulées en raison de la réduction de la pression exercée sur eux par le métal en cours de solidification.
Une fois que la pièce moulée a refroidi à la température souhaitée, le moule peut être ouvert. A ce stade, les tiges métalliques sont retirées et les pièces moulées sont sorties du moule. Les noyaux de sable sont assommés, les bénéfices, les contremarches et les carottessont coupés et le contrôle de la qualité du produit est effectué, après quoi tout le processus peut être répété.
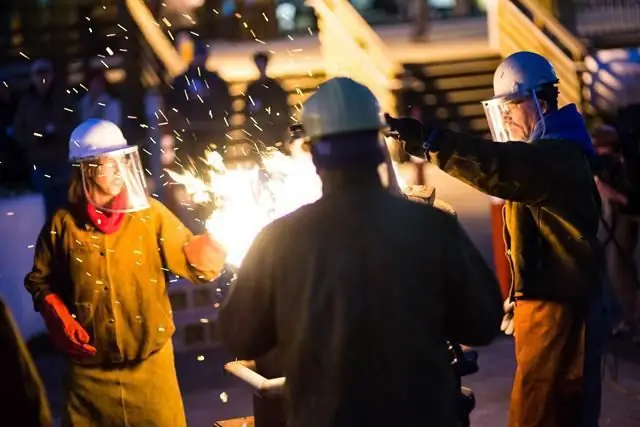
Avant de faire un nouveau moulage, le plan de joint et la surface du moule sont soigneusement examinés. La composition réfractaire est appliquée une ou deux fois par quart de travail, cependant, en cas de délaminage de la surface de travail, il est nécessaire de restaurer la couche. Si le produit est à paroi mince, le moule est fortement refroidi; si la coulée en cours de fabrication était suffisamment massive, le moule pourrait chauffer au-dessus de la température de fonctionnement, puis des systèmes de refroidissement spécialement fournis sont utilisés, de sorte que le moule sera refroidi dans tous les cas avant la prochaine coulée.
La coulée à froid n'implique aucune action complexe et chronophage, à l'exception du processus de refroidissement de la coulée à la température souhaitée. La plupart des opérations peuvent être effectuées automatiquement par des machines, ce qui est l'un des avantages importants de la méthode, mais le principal est que le moule n'est pas une forme unique.